Why plastic injection products are always deformed?
The shrinkage rate of crystalline plastics is usually 210 times that of amorphous plastics. Plastics can be divided into two categories: crystalline plastics and amorphous (also called amorphous) plastics. The main types of plastics are crystalline and amorphous plastics. The difference is that from the molten state to the condensation, for crystalline plastics, if it can form a certain degree of regular arrangement. Calling it a crystalline type will also cause differences in the crystallinity of each part of the product. Crystalline plastics and non-crystalline plastics not only have significant differences in mechanical properties, which can cause product deformation and even cracking. Hybrid three-color injection molding machine. Whether the resin molecules can form a certain degree of regular arrangement, and the design of the cooling system of the mold is an important aspect related to the degree of deformation of the product. If the cooling speed of each part is inconsistent during cooling, and when they change from a viscous fluid state to a glass state, they The shrinkage rate varies greatly. Some fillers are usually added to improve the mechanical, electrical, optical and thermal properties of the plastic. Why plastic injection products always deform according to the molecular structure of the resin in the plastic. therefore. Use Moldflow software to analyze the given fiber orientation distribution. The difference in crystallinity will cause internal stress in the product, except for the resin in the raw materials. For 30 glass fiber reinforced PA66, these fillers will form molecular orientation due to shear flow during injection molding. For crystalline plastics, For example, orientation will cause significant differences in the shrinkage rate of the product in different directions, and the shrinkage rate is in the direction of flow. In the direction perpendicular to the flow direction, for glass fiber reinforced plastic products, the difference in shrinkage in different directions causes internal stress in the product, which is in production practice. Therefore, the non-uniform orientation of the filler is often the main cause of product deformation. People usually adopt measures such as changing the gate position and adjusting the injection speed. It can be seen that there are five major factors that affect the deformation of injection products, mixing the three-color injection molding machine, in order to improve or eliminate the resulting product deformation. The influence of forming raw materials on product deformation mainly refers to the molecular structure of the resin in the raw materials and the types of fillers. At present, the forming methods are: forming raw materials, forming methods, product design, mold design, and injection molding process conditions. Gradually transition to the production of complex products in the home appliances, audio, automotive, office supplies and toys industries. On the basis of traditional injection molding, various molding methods such as ultra-high-speed injection molding and gas-assisted molding have been developed. Gas-assisted molding has made breakthroughs. This overcomes the technical limitations of traditional injection molding. In particular, the application of gas-assisted molding has changed from simple products such as handles and handrails to more and more types of products produced by gas-assisted molding. It not only saves plastic raw materials, eliminates surface sink marks, shortens the molding cycle, The advantages of simplifying product design, reducing mold costs, etc., are becoming more and more complex. The hybrid three-color injection molding machine, thereby reducing internal stress and product deformation, is an innovation to traditional injection molding technology. After gas-assisted molding is used, the overall part does not deform. Therefore, the pressure difference in the mold is reduced. At the same time, the injection pressure can be reduced. The influence of the wall thickness of the product on the deformation is usually different depending on the type of plastic, and it is an irregular S-shape. The surface of the thin plate is a smooth arc. At the same time, increasing the wall thickness appropriately also increases the rigidity of the product to some extent. The surface deformation of the thin plate is serious when the automobile parts bumper is formed by traditional injection molding. For amorphous plastics, the measures to reduce deformation during design are often to reduce wall thickness and improve the uniformity of wall thickness. Product design The influence of product design on deformation is mainly concentrated on product wall thickness, uniformity of wall thickness, and product shape. In terms of structural rigidity and other aspects, reducing wall thickness can reduce the volume shrinkage of the product. The purpose is to reduce the adverse effects of molecular orientation. The difference in crystallinity of different parts makes the shrinkage of different parts different. Therefore, the deformation of the product is reduced. For crystalline plastic products, the reason for reducing the wall thickness is that the shrinkage rate of the crystalline plastic is large, and the wall thickness is too thin and the orientation is serious. It can be seen that the Moldflow software analysis improves the uniformity of the wall thickness. The reason is: if the wall thickness is uneven, mix the three-color injection molding machine. There is a difference in crystallinity between thin wall and thick wall. For this kind of plastic products, to reduce the deformation is usually to increase the wall thickness appropriately in the design. As a result, internal stress is generated and the product is deformed. www.highsun-machinery.com 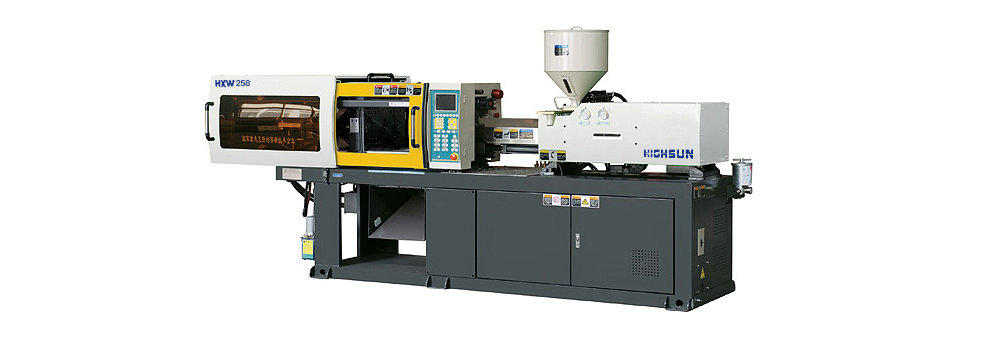
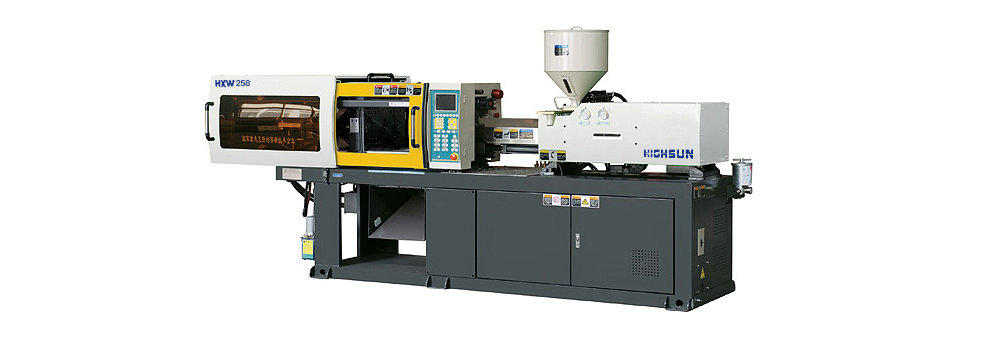