What is the design method of the variable pump injection molding machine?
Variable-pump injection molding machines are designed in such a way that they allow for the complete removal of the material being worked upon from a conventional closed loop. When pumping, the rotary screw pumps the material through a dielectric chamber. This chamber keeps the material from slipping down while the pump rotates. As the rotary screw pump operates on the positive displacement, it ensures that the material remains in its original position and therefore there is no chance of slipping off the sides of the dielectric chamber. To get the best results in terms of precision, a variable displacement pump needs to have an accurate setting mechanism such as the variable speed controller (VSPC). This is one of the most important components of the machine, because it controls the speed and the flow of the pump. The material passes through the dielectric sleeve and then goes into the pump. To get the best-fitting parts for the machine, it is advisable to work with a reputed and experienced supplier. They will help you to determine the exact specification required for your project and will help you to make the necessary changes to get the best output. A number of online shops are selling high quality pump machines. Most of these shops provide the customers with the best possible information regarding pricing and discounts offered on the products. Some of the shops also offer free delivery to their client's premises. While purchasing the machine, make sure to check the parts compatibility and check whether the machine works perfectly with the specific part. This will ensure that you get the best possible output and hence, enjoy making different types of moldings.
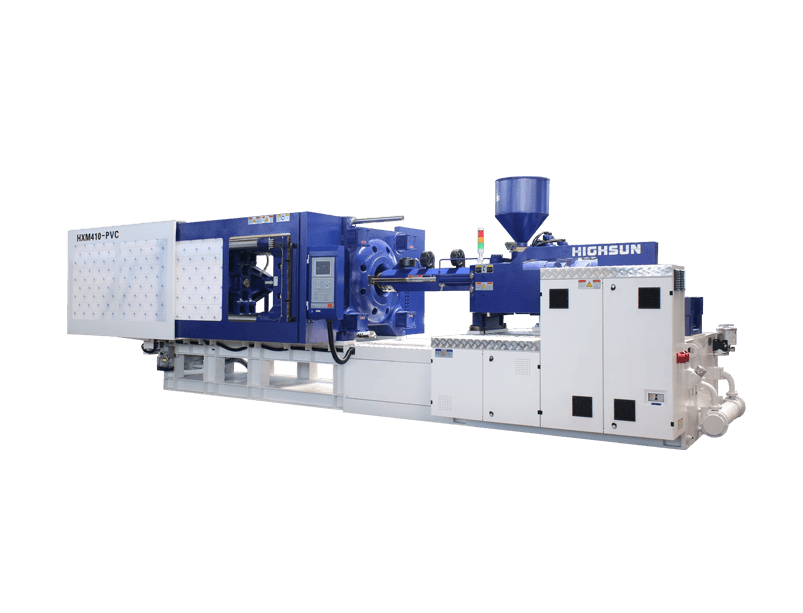