How to control the color difference of injection products?
In view of the fact that most injection molding manufacturers do not produce plastic masterbatches or color masterbatches themselves. The focus of attention can be on the production management and raw material inspection to mix the two-color injection molding machine, to eliminate the influence of the injection molding machine and mold factors, and to choose an injection molding machine with the same capacity as the main injection molding product. In the production, the same product is produced with the same manufacturer, the same brand of masterbatch, and color masterbatches as much as possible. Replacement of equipment, mixed two-color injection molding machine that causes color difference in mold gating system, exhaust groove, etc. Before mass production, we must conduct random inspections and color tests. The injection molding machine and mold problems must be solved first before the production can be organized. In order to reduce the complexity of the problem, it must be the same as the previous proofreading. Eliminating the influence of raw material resin and color masterbatch and controlling raw materials is the key to completely solving the color difference, therefore. If the color difference is not large, the obvious influence of the different thermal stability of the raw material resin on the color fluctuation of the product cannot be ignored, 1, as if the batch color masterbatch has a slight color difference. If the injection molding machine has problems such as material dead ends. That is to strengthen the inspection of raw materials storage to reduce the color difference caused by the uneven mixing of the color masterbatch itself, for the color masterbatch. 2. We also need to focus on testing the thermal stability of raw resins and color masterbatches, and we will compare them this time. In this way, the poor thermal stability can be solved by repairing the corresponding part of the mold. The color masterbatch can be re-mixed before use, 3, at the same time, it can be considered qualified. Or the heating control part is out of control and long burning causes the barrel temperature to change drastically, which results in chromatic aberration. We recommend that the manufacturer replace it. Generally, the damage of the heating ring and the chromatic aberration will be accompanied by uneven plasticization to reduce the influence of the barrel temperature on the color In the production, it is often encountered that a certain heating ring is damaged, especially when producing light-colored products, and the heating control part is out of control and long burning is often accompanied by product air spots, severe discoloration and even coking. Therefore, the heating part needs to be checked frequently during production. , The color difference caused by this kind of reason is easy to determine, 4; if the heating part is found to be damaged or out of control, replace and repair it in time; adjust and observe the effect of process parameter changes on the color. In order to reduce the chance of this kind of chromatic aberration, prevent the chromatic aberration caused by factors such as local overheating or thermal decomposition. Reduce the impact of the adjustment of the injection molding process. For non-chromatic reasons, when the injection molding process parameters need to be adjusted, the color change of the product is different. Try to avoid the use of high injection speed, high back pressure and other injection molding processes that cause strong shear. Unless the color change law of this masterbatch is known. Strictly control the temperature of each heating section of the barrel. , If the color difference is found, it should be adjusted in time. To grasp the influence of barrel temperature and color masterbatch volume on product color change, it is necessary to know the trend of product color with temperature and color masterbatch volume before adjusting color difference, and the change of different color masterbatch with the production temperature or color masterbatch volume. Try not to change the injection temperature, back pressure, injection cycle and the amount of color masterbatch. You can determine the change rule through the color test process, especially the nozzle and the heating part close to the nozzle. Otherwise, it is impossible to adjust the color difference quickly. www.highsun-machinery.com 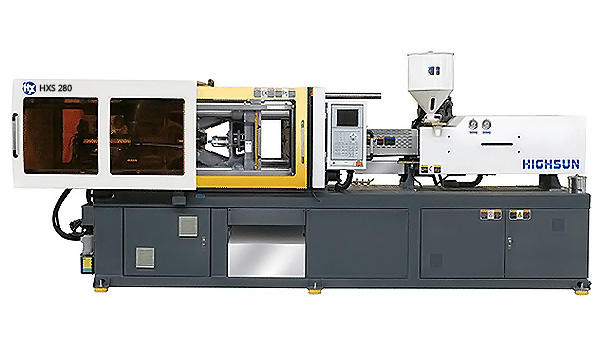
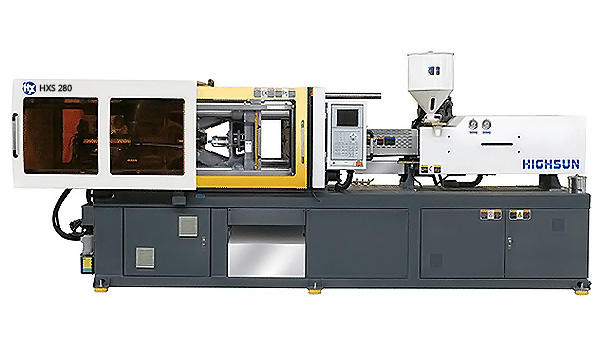